Lightning Spikes
Role Module Designer
Duration 3 weeks
Tools Rhino, Adobe InDesign and Illustrator, Laser Cutting
Context
Lightning Spikes is a modular light fixture crafted from laser-cut wood veneer, diffuse paper, and a custom armature. Collaborating with a team of two peers, I took the lead in designing the modular components of the fixture using Rhino, ensuring that we had variations that created a field condition.
​
This project focused on designing modular components with at least three variations that could be arranged in multiple ways to create a dynamic field condition. It is also a way to explore new materials through the use of laser cutting.


01
Inspiration
To start, we explored projects from design studios and reflected on our previous work for inspiration. We were particularly drawn to Chrysalis (III) by Matsys Design, which became our precedent. Building on this and a prior project by one of my teammates, we decided to design a wood veneer light fixture. Aiming to create a spherical form, we structured the modular design around an icosahedron shape.
02
Iterative Process
Using an icosahedron as a framework, I explored different forms around a triangle base. Balancing seamless geometry with variation, I chose to have the variation element through adjustments like varying side opening sizes, altering top openings, and modifying protrusion depths. To amplify light interplay and texture, I integrated perforated edges and intricate patterns, creating texture and visual intrigue.
​
Finalizing the initial design, we tested it physically by laser-cutting the modules from thick paper. This helped us refine the module layout to achieve the desired look and functionality. Through iterative revisions and laser cutting, we ensured the modules met the project's parameters and was true to what we wanted to achieve. We also determined how the modules would connect to the armature, adding angled folds to secure them in place. Some features, like perforated lines, were excluded from the final design due to the fragility of wood veneer and limited visual impact. Alongside prototyping, we conducted light studies with various types of paper and finalized the custom armature design.
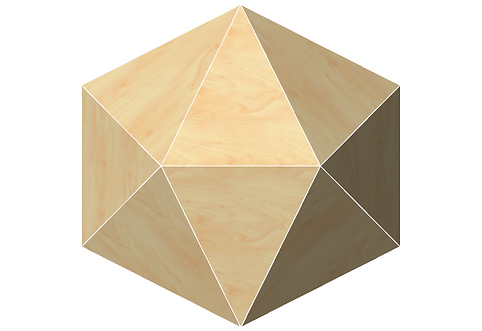
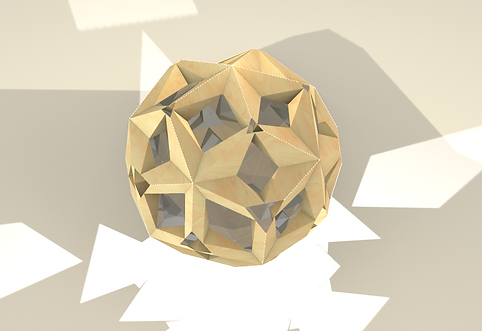

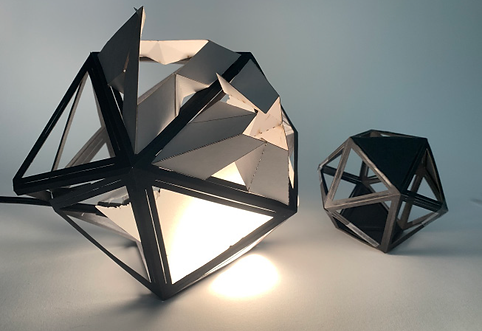



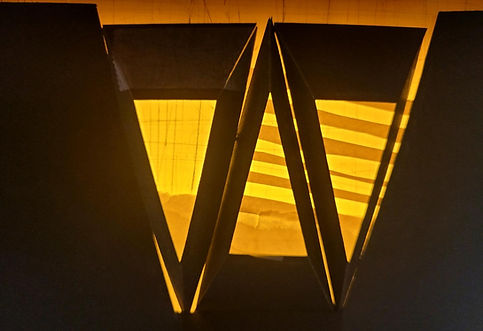
03
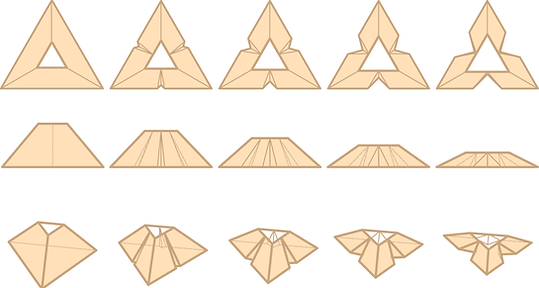
Final Modules
After iterative testing, I refined the design to five final modules, each varying in protrusion, openings, and side indentations. The sequence transitions from a module with the longest protrusion and smallest opening to one with the largest opening, deepest indentation, and shortest protrusion. This reversible gradient effect guides the eye along the fixture, highlighting the interplay of form and openness.


04
Assembly
We laser-cutted the modules using a file with three color-coded engraving depths: blue for cutting, green for deep engraving, and magenta for shallow engraving. The deep engrave was essential for creating side openings, allowing the wood veneer to fold smoothly, especially where folds were close together. Each module included an extra flap for seamless 2D-to-3D assembly. My teammates and I then attached the modules to the custom laser-cut armature with diffused paper. Finally, we inserted a lightbulb, bringing the fixture to life.

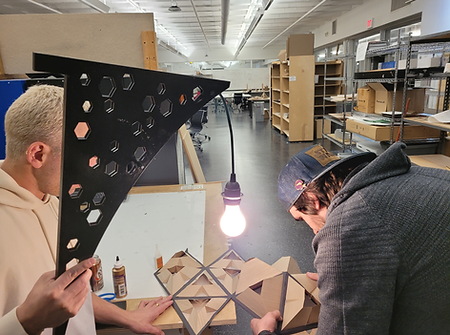
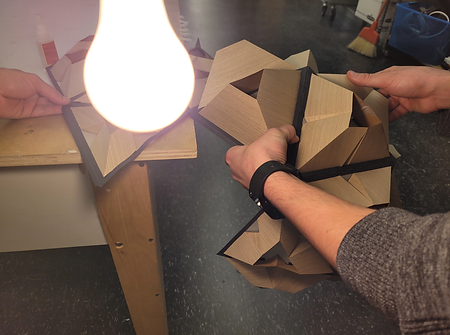
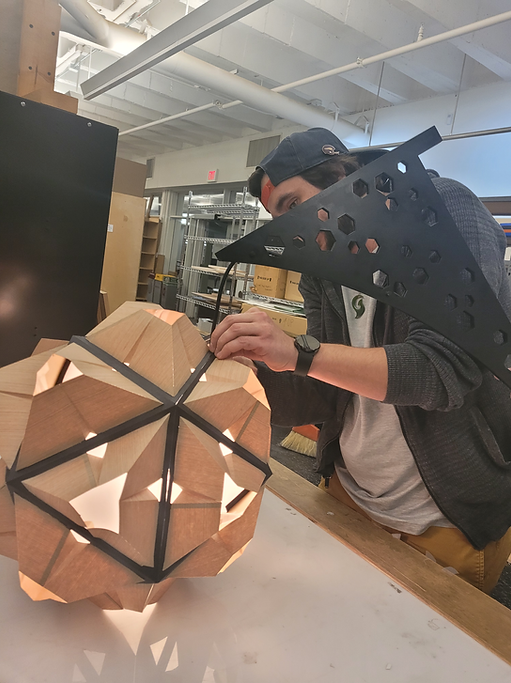
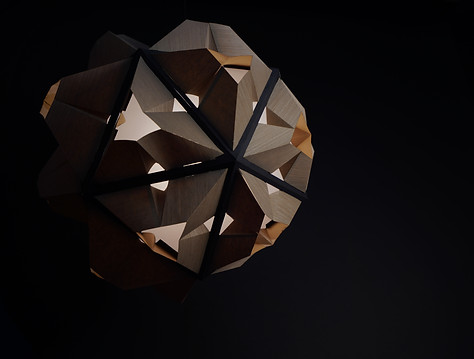
05
Lightning Spikes
While I was familiar with Rhino and had some experience with laser cutting, this project introduced me to working with wood veneer and designing a light fixture. It pushed me to experiment with materiality and fabrication, expanding my skills in both design and execution. In just three weeks, we met the project criteria within its constraints, and I am satisfied with the results. Given more time, I would refine the modules and diffused paper to create a more intentional interplay of light and shadow, further enhancing the fixture’s overall impact.

